Support Services for Offshore Platform
We have the capability for providing support services for offshore platforms and for Rig Preparation works. We have undertaken a contract during the year 2022-23 with Cairn India Ltd for support services for their offshore platforms and deploying suitable manpower on contract basis and provided following services.
- Services (Instruments Installation, cable tray work, cable laying, glanding, termination, SS tubing for well hydraulic lines and PT, PSHL, PSH impulse tubing) required for the four wells, for well surface facility hook up:
- Platform Modification works and Rig Preparation works – Existing platform modification works for conductor drive, adopter and well head installation etc.
- Existing structure modifications and grating removal ,grating installations. Chequered plate removal and plate installation. Piping removals if any obstruction, Instrument supports, Cable tray supports etc.
- Piping pre fabrication, Blasting and three coat Paint, erection, hydro test, radiography, piping support installation, piping tie in ,NRV, Choke valves, valve installation etc.
- Scaffolding Installation and Removal
- Platform Engineer (Process) and Platform riggers for Production support.
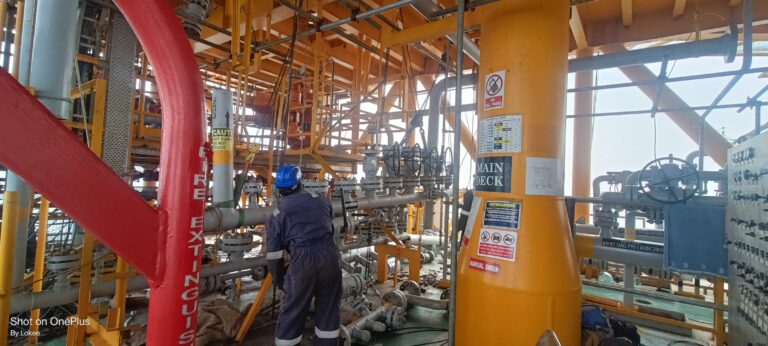
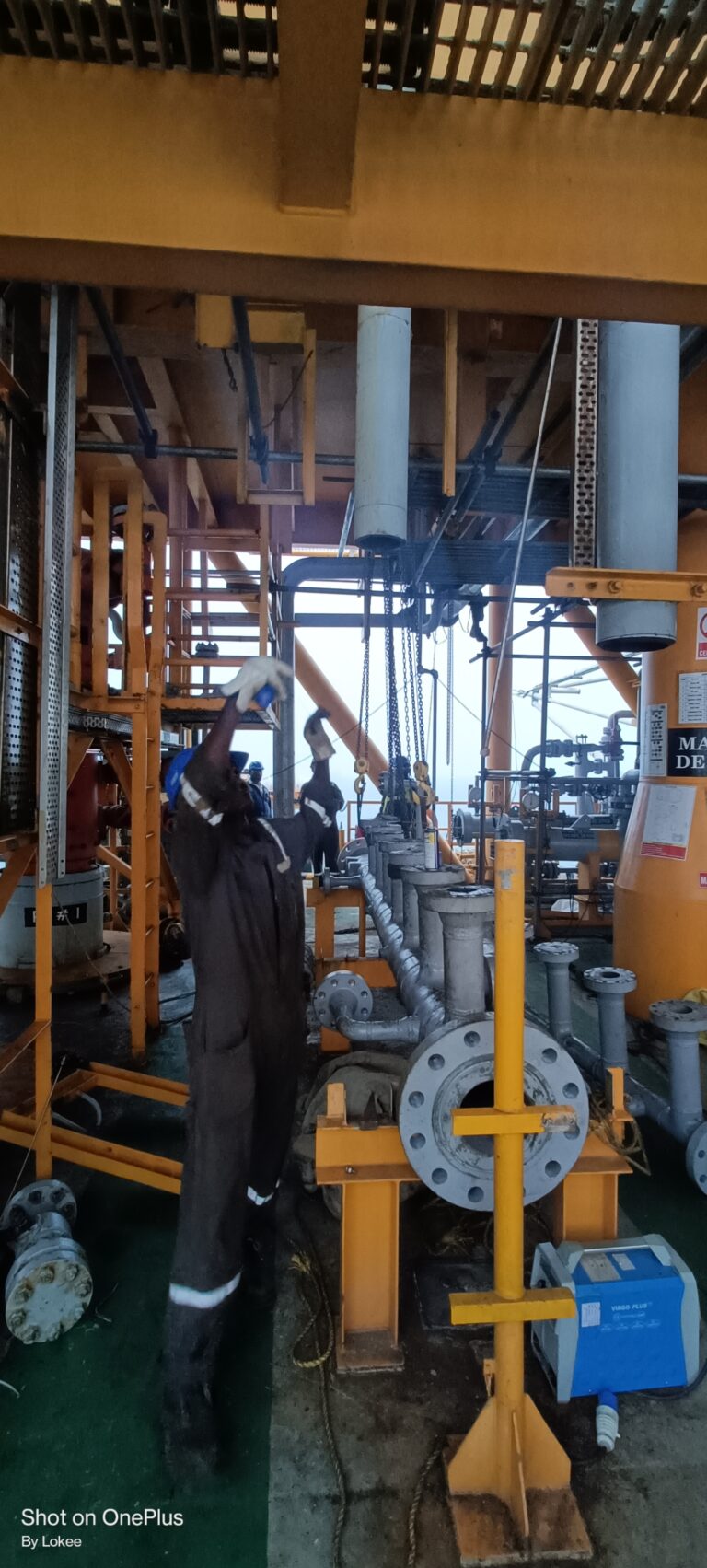
Services for SBM
We have undertaken few services for Single Point/Buoy Mooring System (SBM) . The Cam Locks for the mooring system required renewal of cams. The cams were repaired by Re Tapping of threads on Cam Frame, Machining of threads on cams for adjustment of Locking Height and Fitment of New Cams on Cam Locks Frame and fitment inspection (05 Nos of Cams on each Frame). Renewal/servicing of cam lock frame and outer Ring of 1.5 Inch dia pipe.
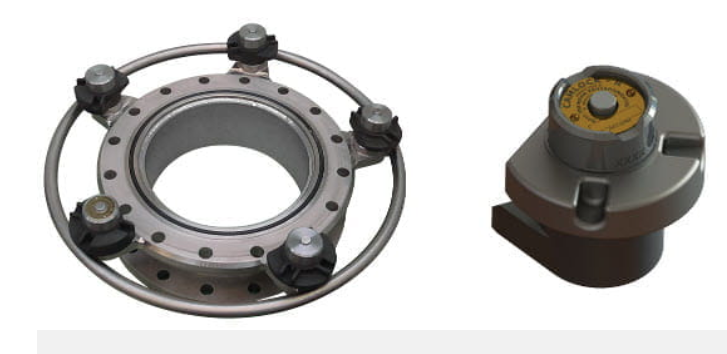
The Dunlop hoses are pressure and vacuum tested. We have undertaken testing of the complete Dunlop hoses at Bhogat on two occasions in afloat insitu condition. For this we have used the dye penetrant for checking for leaks if any during the pressure testing. The following procedure was adopted for leak test of these hoses.
Pressurizing Procedures
1⁄2” hose shall be connected from the pressure pump to the 1⁄2” connection in the blind flange installed at the tanker end of the floating hose string.
High Point vent valve wase left open, until the trapped air bubbles were released from the system.
Pressure in the system was continuously monitored from Pressure Gauges on the loading line and on the blinded flange of the floating hose.
Vent was closed and raised pressure to 50% of leak test pressure i.e., 9.5 bar, held for 30 min and then de-pressurized. The system was then re-pressurized and depressurized 2 to 3 times (with a hold period of 15 to 20 minutes every time) up to 50% of test pressure to allow for hose expansion.
Leaks in the system was identified by the observation of the dye at the leak location.
Pressure was then increased to system leak test pressure of 19.0 bar . Upon reaching the test pressure (i.e. 19 bar) pumping was stopped, test section isolated, 1⁄2” hose was isolated and the pressure will be held for a period of 3 hours or amount of time to inspect each hose and joint , without additional pumping.
All pressurization and test hold periods was monitored and recorded every 15 minutes by means of pressure gauge & pressure recorder installed on the blind flange attend of floating hose.
In case pressure of the system was dropping, then valves at the buoy were closed to pin point the pressure loss section. Calibrated pressure gauges were installed at 2” tap offs the buoy for identifying the leaking section.
Seawater with 600 ppm inhibitor and sea dye was used for filling and leak test activity.
Pressure Gauges were continuously monitored to check any blockage in the system even when the vent valve is kept open
Depressurization
Upon successful completion of the pressure test, connect flexible hoses were connected depending on the out flow rate required and tied them to a solid support such as a channel or a platform. Depressurization was commenced and gradually increased the rate not exceeding 2 burg per minute.
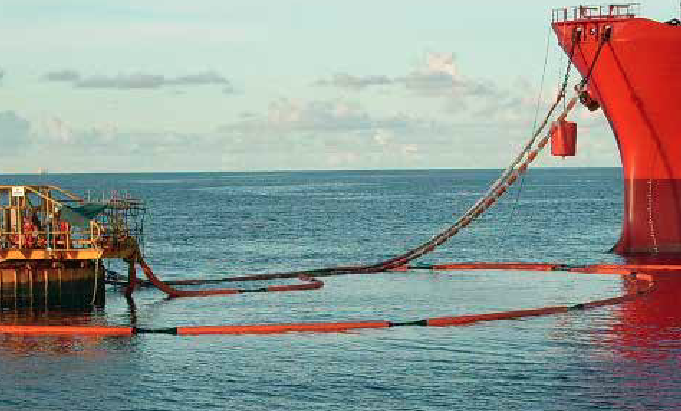
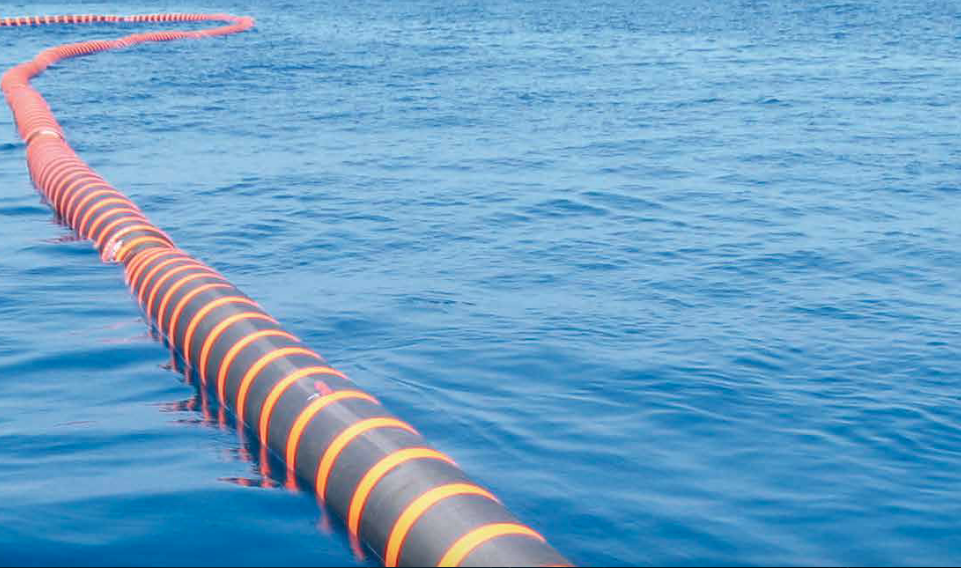